What Is Closed-Loop Manufacturing?
While some environmental terms are well-known and relatively easy to understand, like ‘biodegradable’, ‘compostable’, or ‘sustainable’, the phrase ‘closed-loop manufacturing’ is not as commonplace.
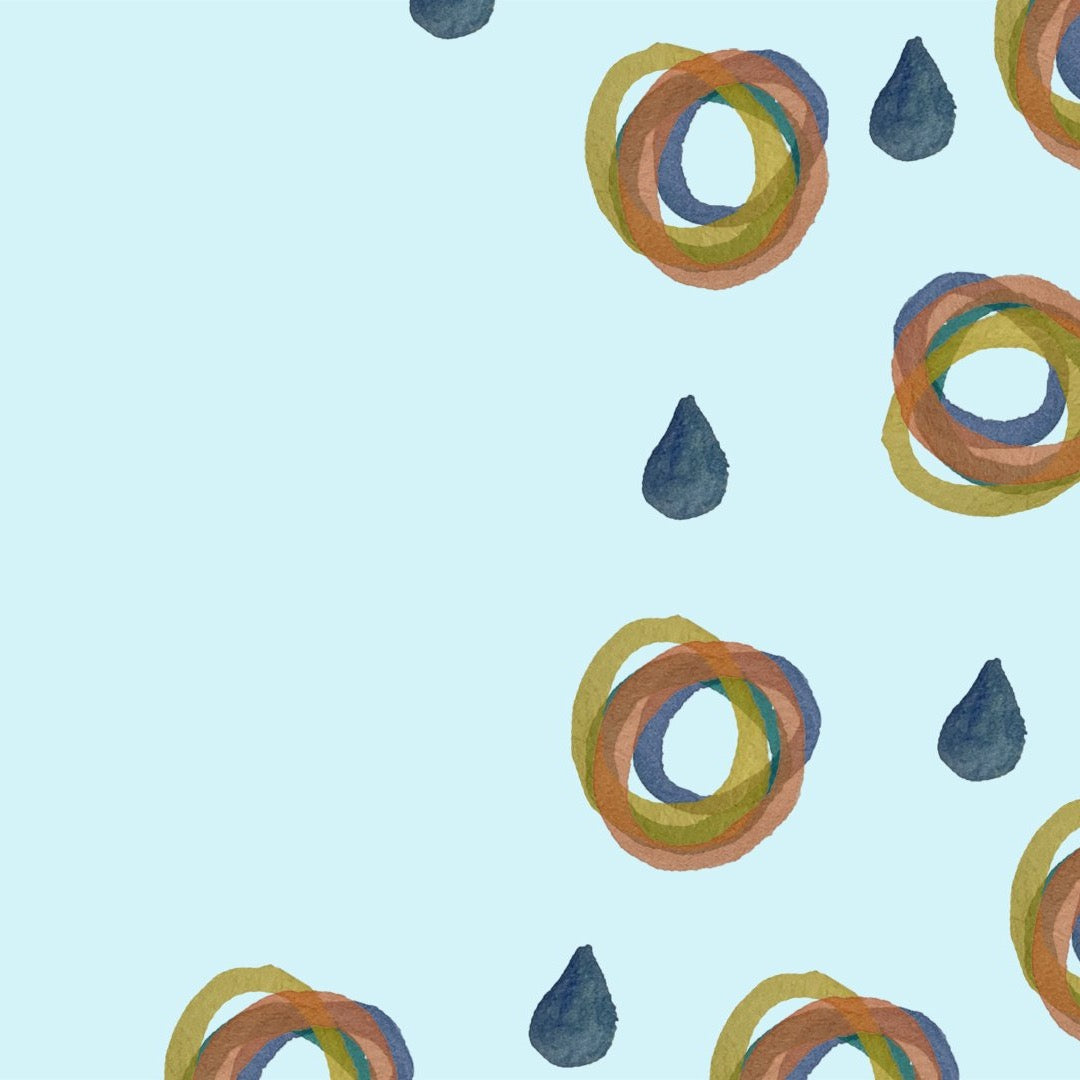
Bearassentials
Closed-loop manufacturing processes, also known as the circular economy, mean that the materials used in production can and will be recycled—able to be reused again and again as they’re made to avoid the eco-unfriendly landfill designation.
Our Tree Napper uses the tree fabric, TENCEL™, which is created with a closed-loop system that incorporates raw wood pulp from sustainably sourced eucalyptus trees—sustainable, super soft, and highly breathable!
Even if companies aren’t able to become completely closed-loop, there are many smaller steps within the supply chain that can be managed to help improve the environment as a whole.
Did you know?
Around 1966, Kenneth Boulding's essay "The Economics of the Coming Spaceship Earth” was cited by many as the first expression of the "circular economy". While it took longer than we’d have liked, it’s good to see brands adopting these practices.
While some environmental terms are well-known and relatively easy to understand, like ‘biodegradable’, ‘compostable’, or ‘sustainable’, the phrase ‘closed-loop manufacturing’ is not as commonplace. Put simply, closed-loop manufacturing means that the materials used in production can be reused. Closing the loop entails that any post-consumer waste is recollected and reused to start the process all over again. In this method, natural resources are conserved, which is a huge win for the environment.
Closed-loop manufacturing is sometimes used interchangeably with ‘circular economy’. The loops and circles in their names make it easy to visualize how the systems work. Instead of a straight line from materials to production to purchase to landfill, the circular economy ensures these products aren’t just used once. Their materials can be reborn into something new, which keeps the loops and circles going round and round.
A closed-loop system you may already be familiar with is recycling, given its iconic symbol featuring arrows chasing one another in a complete and closed, circular loop. When a product or item has served its purpose, the goal is that it can restart its life again with fewer environmental impacts.

Photo by Noah Buscher on Unsplash
How Does Closed-Loop Manufacturing Work?
Let’s go back to the recycling example and imagine an aluminum can that you just finished drinking out of. After tossing that can in your recycling bin, it travels to a treatment plant and gets sorted and cleaned up. The aluminum gets re-melted and formed into large blocks. From there, those blocks are rolled out and reformed into cans or other shapes. That little aluminum can you recycled, becomes ready to go be reinserted into the world as another aluminum product in as few as six weeks. The process repeats indefinitely, thus fulfilling the closed-loop production system. But, this process is all dependent on the consumer, AKA you! Don’t break the loop by tossing it in the trash and always look to purchase post-consumer recycled products.
Materials like aluminum and glass can be recycled over and over again, which reduces the need for sourcing new materials. The reuse of glass is even quicker than aluminum. A glass bottle can be used, recycled, and remade into a new glass container on the shelf within 30 days. Now that’s a quick turnaround!
Closed-loop systems don’t even have to recreate the same product they originated from. For example, Patagonia uses plastic soda bottles to create some of their recycled polyester clothes and Allbirds footwear uses water bottles to form their shoelaces. Very, very resourceful, no?
Let’s Talk About Tencel™
TENCEL™ Lyocell is the eco-friendly tree fabric that makes up our Tree Napper blankets. The material is sourced from sustainably grown raw eucalyptus or beechwood, which employs a closed-loop system. The fiber is made by dissolving the wood pulp and then drying it through spinning. The reason why it’s considered closed-loop is that they’re able to recover and reuse 99% of the solvent used to spin the fiber. This special process utilizes 10 times less water and produces minimal waste and emissions compared to the production of a conventional material.
Once the fiber is fully treated and spun into yarn, it becomes the ultimate breathable and soft fabric, making it the perfect fabric to be woven into our Tree Nappers. Lastly, because the TENCEL™ fibers are made from trees that lived in sustainable forests, the material is fully biodegradable and compostable. When it decomposes back into the earth, the cycle starts all over again—perpetuating the beauty of closed-loop production systems.

Photo by Etienne Delorieux on Unsplash
The eucalyptus trees that TENCEL™ is created from, which are responsibly farmed in Austria, don’t need any pesticides or irrigation to grow, which reduces the environmental impact of resourcing from them. A half-acre of otherwise unusable forest can provide enough eucalyptus trees to produce an entire ton of TENCEL™ material (that’s a lot of Tree Nappers!).
How Does Bearaby Close The Loop?
The number one way we realize closed-loop manufacturing is through the use of TENCEL™ tree fabric, which is the most sustainable way to create our best weighted blankets at this point. We also do our part by using recycled and reusable materials in our packaging—plastic-free and materially minimal remains our approach. All we ask is that you continue the momentous process by recycling your packaging as well.
Other Closed-Loop Companies
Certain companies, some small and some large, have been awakened to the beauty of utilizing closed-loop systems in their production practices. Closed Loop Partners invests in companies that employ closed-loop production and sustainability, like advanced recycling technologies, for instance. They anticipate that the sustainable businesses they invest in will reduce greenhouse gas emissions by 36 million metric tons of CO2 by the year 2030. We hope Mother Nature is proud that we’re making progress.
One example of an eco-friendly business is Kona Brewing Company in Hawaii, which recycles its leftover grains from brewing into pizza crusts. Kona also collects condensation from their air conditioning, which then gets put back into their irrigation systems and gardens. Sierra Nevada, the well-known California beer brand, also uses closed-loop practices by composting brewery waste into the soil used to grow hops and barley, which then creates more beer. Cheers to that!
Even corporate giants, like Starbucks, Nike, and Levi Strauss, are becoming increasingly more eco-friendly by adopting some closed-loop processes. While not perfect, every additional step to help the environment is welcomed with open arms. Starbucks has been grinding into gear (pun intended) to create a more sustainable and recyclable version of the to-go coffee cup. It’s estimated that 50 billion paper coffee cups go to the landfill each and every year, and from the United States alone! Let’s hope for a more sustainable version soon, but in the meantime, BYOC (Bring Your Own Cup) when you can.
